Spinning product processing is a process of processing various metal materials into a spinning part. There are also many kinds of such methods. Among them, there are the difference of strong CNC spinning process and ordinary spinning process. This article introduces the spinning technology. Basic knowledge, through four aspects to help you easily understand the basis of the spinning process, even beginners can understand.
1.Process classification of spinning technology
2.Analysis of Metal Spinning Principle
3.The difference with conventional spinning and strong spinning
4.Metal Spinning Process Flow
1.Process classification of spinning technology
Spinning technology means that deformed blank plate mount on the spindle end of the mandrel. and, follows the rotation of the main spindle and the mandrel (it is also possible to rotate the rollers around it), in which the rollers performs a feed motion relative to the mandrel. And, spinning the blank plate gradually by the spinning force which generated by the contact of the rollers with the blank plate.
The metal spinning machine can perform spinning, seaming, flange spinning, necking, shear forming, trimming, etc.
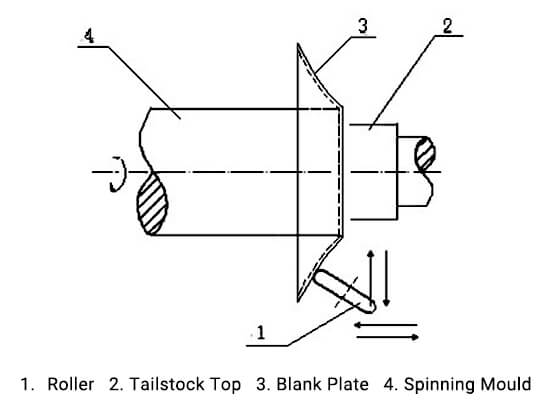
According to the wall thickness variation of the blank plate during the spinning process, the spinning technology divides into two categories: conventional spinning (the thickness is constant) and power spinning (the thickness is varying). So, the Conventional spinning is widely used in the deep drawing, necking and expanding of parts.
According to the type of spinning parts and the difference of metal deformation mechanism, the power spinning divides into cone-shape spinning (shearing spinning) and cylindrical-shape spinning (extrusion spinning).
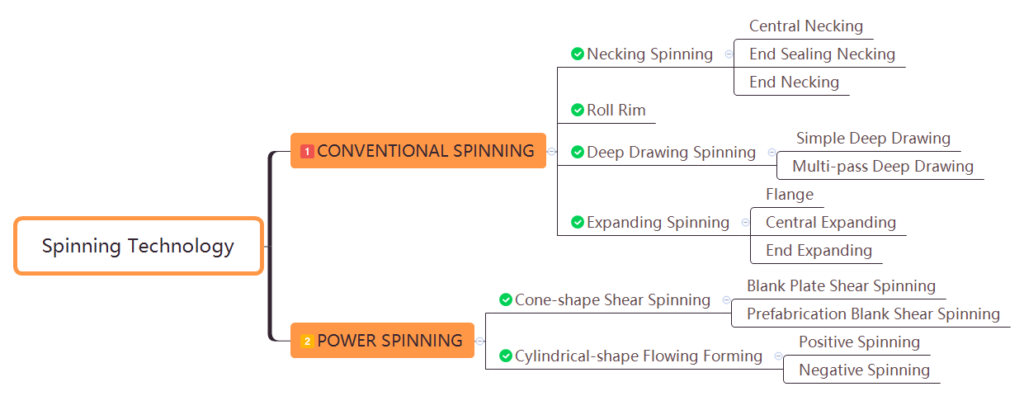
2.Analysis of Metal Spinning Principle
With regard to conventional spinning, the thickness of the blank does not change much during the spinning process. and, the blank contracted or elongated in the circumferential direction and the radial direction to complete the forming of the workpiece, formed by changing the diameter of the sheet.
So, it is suite to process thin-walled rotary bodies with non-cutting deformation. And, the process also causes a slight thickness change. Partial thinning and instability are likely to occur during the spin forming process, so that is better to increase the spinning steps to avoid defects.
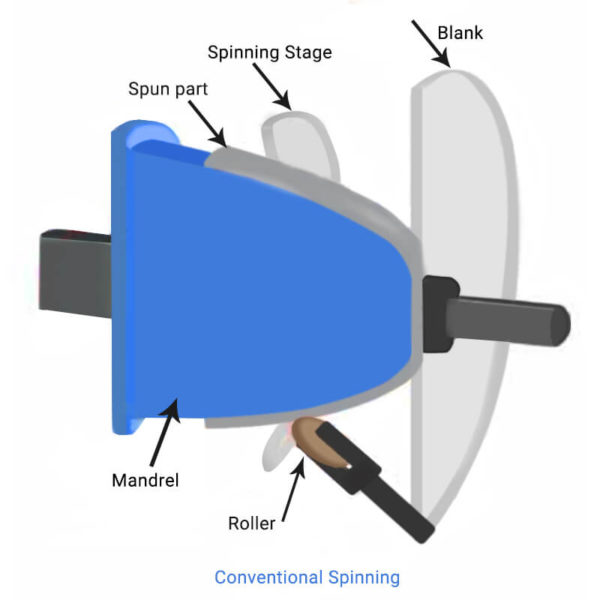
Power spinning can also name thinning spinning. After spinning, not only the thickness of the blank changed, but also its size, shape, and performance changed. therefore, the thickness of the part after power spinning will be less than the thickness before spinning.
Power spinning can divide into two types, shear spinning, extrusion spinning. Similarity, shear spinning often spun blank plates, such as cones, hemispheres, and parabolas. extrusion spinning often spun the cylindrical workpiece. When spun the composite part, can simultaneously adopt two spinning processes.
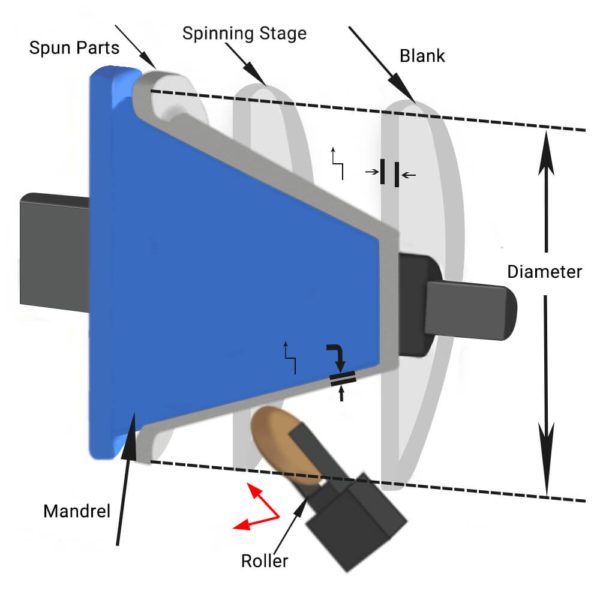
3.The difference with conventional spinning and strong spinning
The type division of strong spinning can divide into positive spinning and negative spinning. according to the flow direction of the blank metal relative to the feeding direction of the roller.
The flow direction of the reference material determines the positive spinning and negative spinning. So, the advantage of the positive spinning is that the material instability is not often present during the spinning process. and, the metal accumulation is rare.
Therefore, when the spun the ovality part, positive spinning is the best choice. consequently, the disadvantage of positive spinning is that the thickness reduction ratio is likely to occur during the spinning process, which causes a relative slip between the blank and the mandrel.
The advantage of negative spinning is that even if the length of the mandrel is not enough or the stroke of the carriage is too short, it can spin out a longer workpiece. The disadvantage of negative spinning is that metal accumulation often occurs during the spinning process, and the expansion is more serious.
Conventional spinning only changes the shape of the blank without substantially changing its wall thickness. but, power spinning not only changes the shape of the blank but also significantly changes the wall thickness of the blank.
Type | Drawing | ||
Conventional spinning | Necking Spinning | ![]() |
|
Expanding Spinning | ![]() |
||
Deep Drawing Spinning | ![]() |
||
Power Spinning | Shear Spinning | ![]() |
|
Cylindrical Thinning Spinning | Positive Spinning | ![]() |
|
Negative Spinning | ![]() |
4.Metal Spinning Process Flow
The current CNC metal spinning machine can realize one-time clamping production. therefore, the processing methods are conventional spinning and power spinning. The general spinning process is as follows:
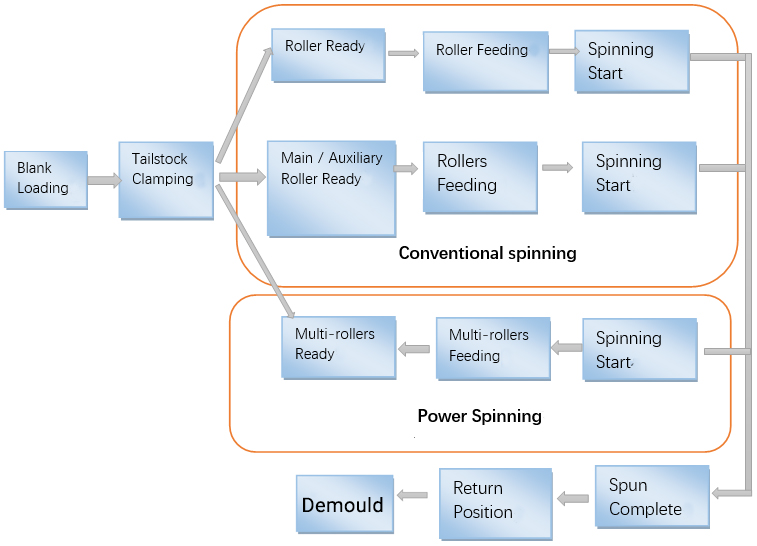
Before spinning, the spindle fixes core by a fixture. and, the top of the tail exerts certain clamping force. Meanwhile, The blank fixes on the core die, to clamp the blank with the tail top.
During spinning, the core dies, blank and tail top rotate together with the spindle. and, the main roller and the auxiliary roller feed according to the predetermined feed path.thus realizing the spinning forming process, after the spinning forming, the spindle stops rotating. loosening the clamping force at the top of the tail can separate the spinning part from the core die.
In conclusion, Mastering the spinning processing principle and process flow of the conventional spinning and power spinning. and, clarifying the similarities and differences between them, is the basis for understanding the spinning process technology.